Composition And Configuration Of Concrete Batching Machines In Concrete Mixing Plants
The concrete batching machine of the concrete mixing plant mainly consists of the following key parts.
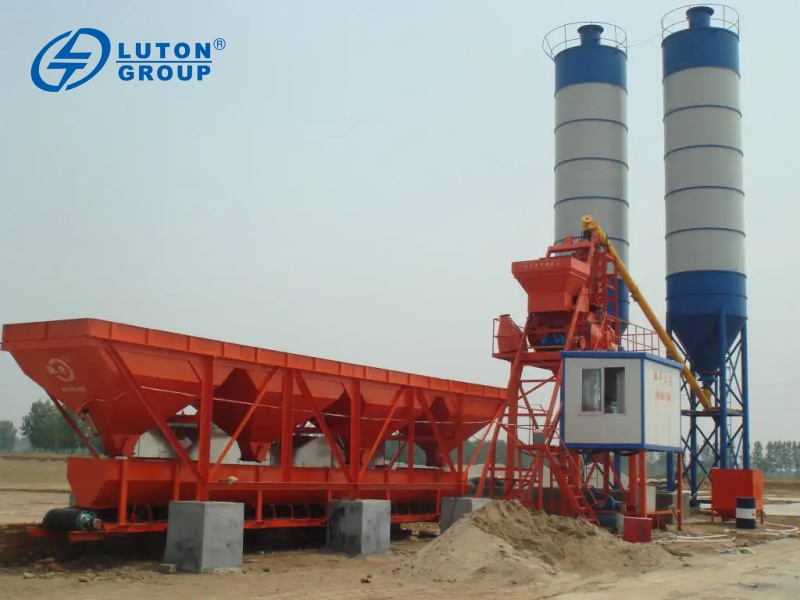
Storage Hopper
This is the basic part of the batching machine, mainly used to store various concrete raw materials, such as stones, sand, cement, etc. Storage hoppers are usually designed with different numbers of compartments to meet the storage needs of different types and quantities of raw materials.
Weighing System
This is the core part of the batching machine, mainly composed of weighing hoppers, suspension devices, weighing sensors, and batching controllers. Its main function is to accurately measure various raw materials and ensure the accuracy of concrete mix proportions.
Feeding System
The feeding system usually consists of a feeding device and a conveying device, responsible for conveying the raw materials from the storage hopper to the weighing hopper in a predetermined proportion and sequence. There may be various forms of feeding, such as belt conveyor feeding and pneumatic feeding.
Electronic Control System
The electronic control system is the “brain” of the batching machine, mainly composed of the batching control instrument and the high-voltage circuit quantity part. It is responsible for controlling the operation of the entire batching machine, including weighing, feeding, display, operation, and completing various automatic batching programs.
In addition, the batching machine may also include other auxiliary components, such as pneumatic butterfly valves, cylinders, vibration machines, etc., to ensure smooth transportation and accurate measurement of raw materials.
When selecting a batching machine, it is necessary to comprehensively consider factors such as actual production scale, site size, and concrete type to ensure that the performance of the batching machine can meet production needs. Meanwhile, proper maintenance and upkeep are also key to ensuring the long-term stable operation of the batching machine.
Taking the HZS90 concrete mixing plant as an example, the specific configuration and technical parameters of its batching machine are as follows.
Configuration
Mixing Machine
The HZS90 mixing plant is usually equipped with the JS1500 forced mixer, which is an efficient and durable mixing machine with a nominal capacity of 1500L, capable of meeting the production needs of large quantities of concrete.
Batching Machine
The model of the HZS90 mixing plant’s batching machine is usually PLD2400, which has strong batching capacity and precise metering system, ensuring accurate proportioning of various raw materials.
Transportation System
Including conveyor belts, screw conveyors, etc., used to transport raw materials from the storage bin to the batching machine and mixing host. The maximum production rate of the screw conveyor can reach 80t/h, ensuring the continuity and stability of raw material supply.
Belt Conveyor
Bandwidth
The bandwidth and thickness of the belt conveyor are determined based on specific application requirements and the scale of the mixing plant, so there is no fixed standard value.
Generally speaking, bandwidth is one of the important parameters of belt conveyor specifications, which directly affects the transportation capacity and applicability of the belt conveyor. According to different application requirements, the bandwidth of the belt conveyor can be selected from various specifications such as 500mm, 650mm, 800mm, 1000mm, 1200mm, 1400mm, 1600mm, etc. The thickness of the belt is usually determined based on factors such as the material, strength, and service life of the belt.
In concrete mixing plants, the selection of belt conveyor speed is usually determined based on specific application scenarios, material properties, and production efficiency requirements. Generally speaking, the belt speed of a belt conveyor should not be too high to prevent material scattering during the conveying process. Therefore, the belt conveyor speed in concrete mixing plants is generally selected within a relatively low range.
Belt Speed
Common belt conveyor speeds include 1.6m/s, 2.0m/s, and 2.5m/s. These speeds can ensure stable and continuous flow of materials during transportation, while avoiding material scattering or blockage caused by excessive speed.
It is worth noting that for materials with large block size or strong wear, as well as when using fixed discharge equipment, low-speed drum belt conveyors should be selected as much as possible. This can reduce the wear and impact of materials during transportation, improve transportation efficiency, and extend the service life of equipment.
Control System
Adopting an intelligent computer control room, it can achieve automated control and monitoring, improve production efficiency and product quality.
Weighing System
Including aggregate weighing system, cement weighing system, fly ash weighing system, water weighing system, and admixture weighing system, these systems can accurately weigh various raw materials, ensuring the accuracy of concrete mix proportion.
Technical Parameters
Theoretical productivity: The theoretical productivity of HZS90 concrete mixing plant is 90m ³/ h. This means that under ideal conditions, the mixing plant can produce 90 cubic meters of concrete per hour.
- Installed Capacity
According to the specific configuration, the installed capacity of the HZS90 mixing plant is usually between 164kW and 194.5kW, depending on the power of the motor, conveying equipment, and control system used.
- Discharge Height
The discharge height is generally between 3.8m and 4.2m, depending on the design and production requirements of the mixing machine.
- Types And Maximum Particle Size Of Aggregates
HZS90 mixing plant is usually able to handle multiple types of aggregates, with the maximum particle size of aggregates Φ 80mm, meeting the needs of different concrete formulas.
- Weighing Range And Accuracy
There are strict regulations for the weighing range and accuracy of various raw materials, such as cement weighing range and accuracy of (0-900) ± 1% kg, to ensure the accuracy of concrete mix proportions.
In summary, the batching machine configuration and technical parameters of the HZS90 concrete mixing plant are designed for efficient, stable, and accurate concrete production, which can meet the requirements of large-scale engineering for concrete quality and yield. Of course, the specific configuration and technical parameters may vary depending on the needs of the manufacturer and customer. It is recommended to consult the manufacturer for detailed technical specifications and performance parameters during actual purchase.
Automatic Control System of Stationary Concrete Batching Plant
In modern construction projects, concrete is the main building material, and its quality and stability of supply are crucial to the success of the project. In order to meet this demand, the stationary concrete batching plant came into being and is equipped with a fully automatic control system to ensure the continuous and efficient production of concrete.
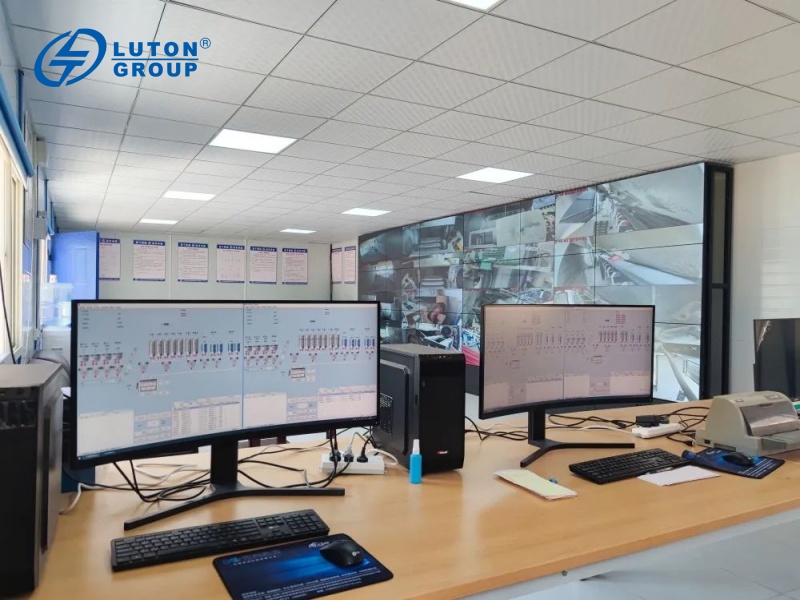
Automatic control system
The automatic control system is the core part of the stationary plant for mixing concrete, which integrates advanced computer technology, sensor technology and communication technology to realize the automatic monitoring and management of the whole process of concrete production. The system can monitor key parameters such as the addition of raw materials, the amount of water, and the mixing time in real time to ensure the quality and performance of concrete. At the same time, the system can also automatically adjust the production parameters to cope with the impact of different seasons and climatic conditions to ensure a stable supply of concrete.
In addition, the fully automatic control system also has a high degree of safety and reliability. It can monitor the operating status of the equipment in real time, find abnormal situations and alarm in time, effectively avoid the occurrence of equipment failures and production accidents. At the same time, the system can also realize remote monitoring and management, which is convenient for managers to know the production status at any time and make timely and accurate decisions.
Advantages of stationary concrete batching plant
The stationary concrete mixing plant from LT GROUP has significant advantages over the traditional mobile mixing equipment. First of all, its production capacity is strong, able to meet the needs of large-scale, continuous concrete production. Secondly, the production efficiency of fixed concrete mixing station is high, which can greatly shorten the production time of concrete and reduce production costs. In addition, due to the use of fully automatic control system, the concrete quality of the fixed concrete mixing plant is more stable and the performance is better.
Another advantage of the stationary concrete mixing plant is environmental protection. It adopts a closed production design, which effectively reduces dust and noise pollution. At the same time, the equipment is also equipped with a waste recycling system, which can reuse the waste generated in the production process, realizing the recycling of resources and environmental protection.
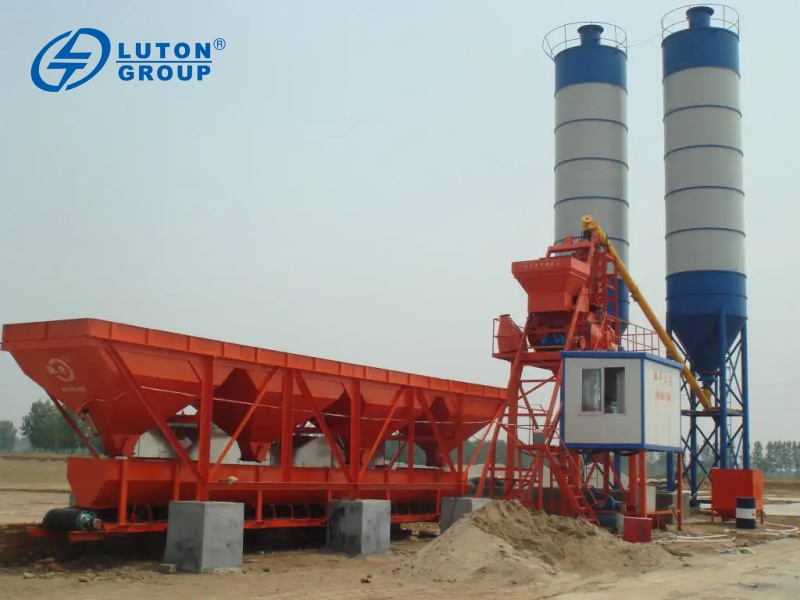
In short, the automatic control system of stationary concrete mixing plant from manufacturers and its unique advantages make it have a wide range of application prospects in the modern construction industry.
What is Colored Asphalt
Colored asphalt, as the name suggests, is a colored asphalt material. It adds dyes of various colors to traditional asphalt materials, making the asphalt surface appear brightly colored. The colored asphalt not only has the advantages of anti-skid, wear resistance, and environmental protection, but also can effectively improve the urban environment and improve the aesthetics of the road.
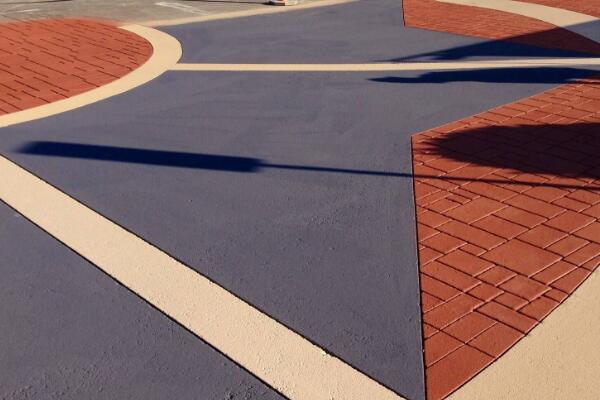
Uses of colored asphalt
1. Beautify the urban environment
Colored asphalt has bright colors and can effectively beautify and decorate the urban environment. Especially in public places such as parks, squares, streets, etc., the colored asphalt can make these places more vivid and beautiful.
Related Post: How to produce asphalt?
2. Improve road safety
Colored asphalt has good reflective properties, which can improve road safety at night or on rainy days. At the same time, because colored asphalt has good anti-skid properties, it can reduce the occurrence of traffic accidents.
3. Environmental protection and energy saving
Colored asphalt is an environmentally friendly and energy-saving material. It can reduce environmental pollution during the production process and does not produce harmful substances during use. In addition, the production cost of colored asphalt is relatively low, which can effectively reduce project costs.
How to use colored asphalt
1. Preparation work before construction
Before construction, the construction site needs to be cleaned and repaired. Especially for damaged floors, repairs and grinding are required to ensure that the colored asphalt can bond well with the ground.
2. Preparation of colored asphalt materials
Colored asphalt materials and dyes are mixed together in a certain proportion according to the required color and quantity. During the mixing process, attention needs to be paid to stirring evenly to avoid uneven colors.
3. Lay colored asphalt pavement
Spread the prepared colored asphalt material evenly on the construction site, and then use a scraper or trowel to smooth it. During the laying process, care needs to be taken to avoid bubbles or hollows.
4. Care and maintenance
After the construction of colored asphalt pavement is completed, care and maintenance are required. Especially in the few days after construction is completed, it is necessary to prevent pedestrians, vehicles, etc. from causing damage to the road surface. In addition, if damage or wear is found, timely repairs and maintenance are required.
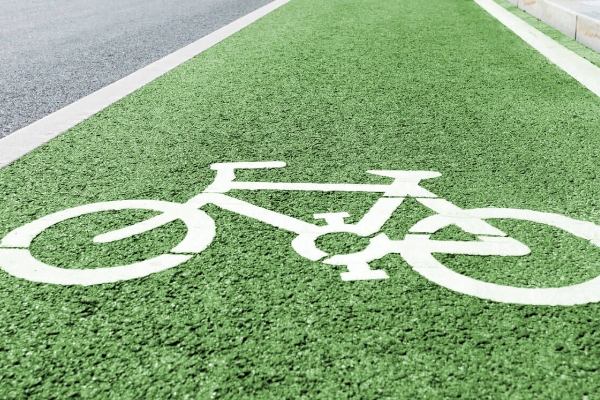
In short, colored asphalt is a new material with many advantages and is widely used in urban construction and beautification. By using colored asphalt materials, the urban environment can be effectively improved, and the safety and aesthetics of roads can be improved. At the same time, the use of colored asphalt materials is also an environmentally friendly and energy-saving choice, which can make a positive contribution to urban construction and development. More types of asphalt, please visit www.ltasphaltplant.com
Brief Introduction on the Development History of Concrete
Concrete is a kind of building material made of cement, sand, stone and water and other raw materials mixed, it has the advantages of high strength, durability, fire, waterproof and so on, so it is widely used in the construction industry. Here is the history of concrete:
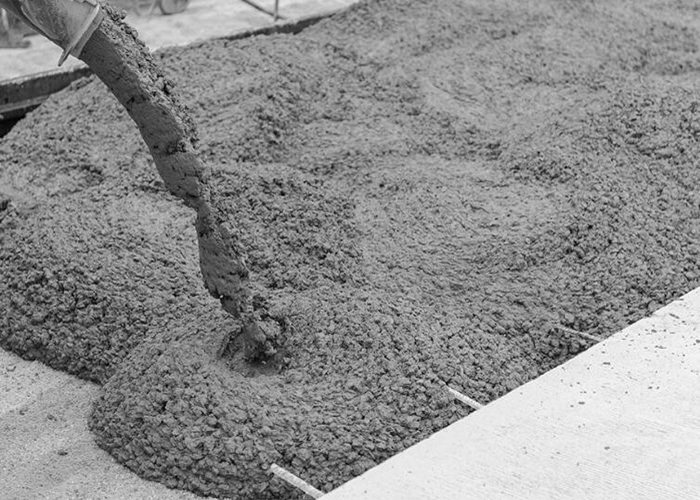
In ancient times, people have begun to use materials like concrete for construction. The Egyptians, for example, began using materials such as lime, clay and sand to make building materials similar to concrete around 3000 BC. In ancient Greece and Rome, concrete was widely used, such as in the construction of huge colosseums and waterways. However, due to the low strength and durability of concrete at the time, the lifespan of the building was also relatively short. Clink on selfloadingconcretemixer.com to learn more.
In the 19th century, people began to study how to improve the strength and durability of concrete. In 1844, Joseph Aspdin of England invented a new type of cement called common cement, which was made by firing limestone and clay. This cement has higher strength and hardness, which makes the performance of the concrete significantly improved.
At the beginning of the 20th century, concrete was more widely used. In 1913, American architect Ernest L. Ransome invented a new type of reinforced concrete structure, which has higher strength and stability, and has become one of the commonly used structural forms in modern architecture. Since then, people have continued to explore the performance and application of concrete, such as adding steel wire, glass fiber and other materials to concrete to improve the tensile strength and durability of concrete.
In recent years, with the continuous development of science and technology, concrete has been more innovative and applied. For example, people began to use equipment to mix the high-performance concrete, self-healing concrete and other new materials, as well as the use of 3D printing and other technologies to manufacture concrete components, making concrete more widely used.
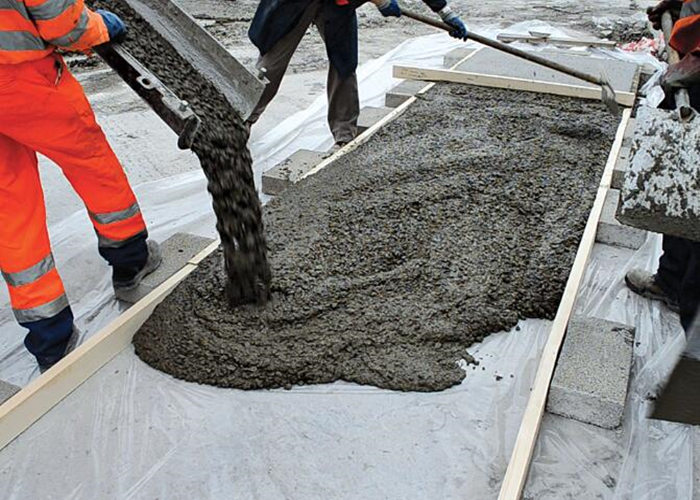
In short, the development of concrete can be traced back to ancient times, after continuous research and innovation, modern concrete has become one of the indispensable materials in the construction industry, and it is also constantly developing and innovating.
Maintenance Of Conveying Cylinder In The Mixing Conveying Pump
Delivery cylinder is an important part of the mixing pump and concrete pump. As a vulnerable part of the pump truck, long-term contact with concrete, and non-obvious part of the pump machine, the daily maintenance is easy to neglect! In the construction process of concrete pump, if used improperly, it is easy to lead to premature damage of some parts, which increase the cost of equipment maintenance, and seriously affect the concrete pouring.
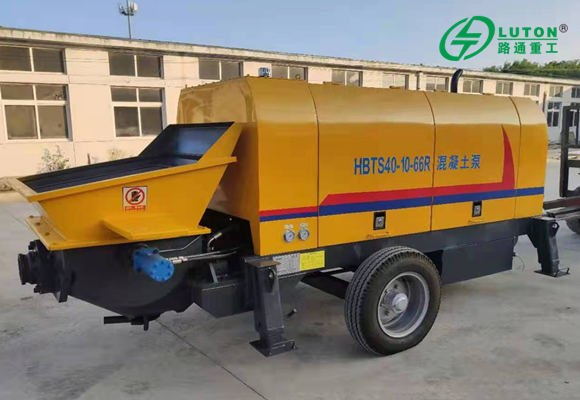
How To Improve The Service Life Of The Delivery Cylinder?
Two Points Need To Be Noted:
Piston and delivery cylinder piston is generally made of polyurethane material, elastic, wear-resistant and other advantages. The inner wall of the delivery cylinder is coated wear-resistant material.
Lubrication mode of the piston and the delivery cylinder is automatic lubrication, each pump, lubrication system filling lubricating oil. Pump operator note:
1.the quality of lithium grease, buy the products of regular manufacturers;
2.Often pay attention to the oil level in the lubricating oil tank, whether there is lithium grease;
3.If the lubrication pipeline or oil distributor is blocked, dredge or replace in time.
Concrete conveying in the process of pumping, operators should often “suppress cylinder” operation, namely when the main cylinder piston running to the end, operate the click button, keep 5~8s, to supplement hydraulic oil in the main closed cylinder (for pump that rely on the proximity switch, keep the proximity switch as close to the side of the main cylinder), to make full use of the travel of the conveying cylinder to avoid local wear of the conveying cylinder.
Operators should also pay close attention to the water tank, once the water is found to be cloudy or sand in the water, indicating that the piston may wear, need to replace the piston in time, otherwise the piston and conveying cylinder will be worn seriously. If the water becomes cloudy soon after replacing the new piston, it indicates that the conveying cylinder has worn out and the conveying cylinder needs to be replaced.
If possible, you can judge whether the conveying cylinder is worn out by measuring the cylinder diameter. Usually, the thickness of the chrome plating layer in the inner wall of the cylinder is only (0.2~0.25) mm. When the cylinder diameter increases (0.45~0.55) mm, it is necessary to replace the conveying cylinder.
There is a cleaning water tank between the conveying cylinder and the main oil cylinder, which is filled with water. Many customers think that as long as there is water, they do not need to replace it too often. The main function of water tank is to cool and reduce the temperature caused by the piston rod and conveying cylinder during working; Another is to clean the piston rod and concrete cylinder of impurities. See here, we should understand the importance of often changing the water body in the water tank.
Special note: many customers think that the water tank is better and can be lubricated, in fact, because the oil floats above the water, hindering the heat dissipation effect of the water, especially when the temperature in summer is high, it should be replaced in time.
Decorative Stamped Concrete
Patterns of Decorative Stamped Concrete
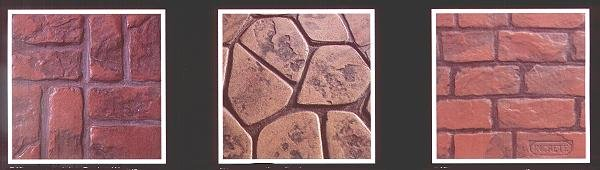
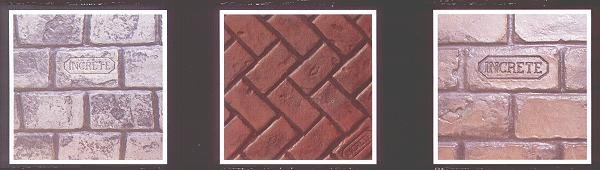
Increte’s unique concept transforms normal concrete into the natural look of slate, granite or stone at a fraction of the cost!
-Freedom of Expression
-Flexibility To create Your Lifestyle
-The Affluent Look At An Affordable Price
-A Myriad of Colors and Designs
-Unlimited Durability
-Perfect for Driveways, Pool Decks, Patios, Streets and Lanais
We Carry All Your Concrete Construction Material Needs
We can carry all your concrete construction materials needs, including building materials, fasteners, wire and steel, hand tools, miscellaneous, power tools, chemicals, and clothing and safety.